Transforming a derelict factory into a vibrant home presents a unique blend of challenges and rewards. This journey requires navigating the complexities of structural rehabilitation, environmental remediation, and meticulous design. From addressing hazardous materials like asbestos and lead paint to upgrading outdated infrastructure and integrating modern amenities, the process demands a multidisciplinary approach, blending engineering prowess with artistic vision.
This narrative delves into the intricacies of this ambitious undertaking, exploring the scientific principles and practical considerations involved in converting a space designed for industrial production into a comfortable and aesthetically pleasing residence.
The transformation necessitates a deep understanding of building codes, a keen eye for design, and a meticulous attention to detail. We will examine the structural integrity of factory buildings, the potential environmental hazards lurking within, and the strategies for mitigating those risks. We will also explore the aesthetic possibilities, showcasing how industrial elements can be creatively integrated into a modern living space.
This detailed exploration will empower aspiring homeowners to confidently navigate the complexities of this unique renovation project.
Challenges of Factory-to-Home Conversion
Transforming a derelict factory into a comfortable and safe residence presents a unique set of challenges, far exceeding those encountered in typical home renovations. The sheer scale of the project, the inherent structural differences between industrial and residential buildings, and the potential presence of hazardous materials all contribute to a complex and potentially costly undertaking. Careful planning, expert consultation, and a thorough understanding of the building’s history are crucial for success.
Structural Challenges in Factory-to-Home Conversions
Factory buildings are designed for heavy industrial use, prioritizing strength and durability over aesthetic appeal or energy efficiency. This often translates to thick concrete walls and floors, massive steel beams, and high ceilings – features that are both advantageous and problematic for residential conversion. While the robust structure can provide a solid foundation, adapting it to residential needs requires careful consideration.
For instance, the large open spaces typical of factories need to be subdivided into smaller, more intimate living areas, requiring the strategic placement of interior walls and the installation of new plumbing, electrical, and HVAC systems. The high ceilings, while offering a sense of grandeur, may lead to increased heating and cooling costs unless properly insulated. Moreover, the original factory design might lack adequate natural light and ventilation, necessitating creative solutions to maximize light penetration and airflow.
Consider, for example, the conversion of a former textile mill in Manchester, England, where the massive window frames were repurposed, and new skylights were installed to create a brighter, more airy living space.
Environmental Hazards in Old Factories and Remediation Methods
Old factories often harbor a range of environmental hazards accumulated over decades of industrial activity. Asbestos, lead-based paint, and various chemical residues are common concerns. Asbestos, a fibrous mineral once widely used for insulation, is a known carcinogen, posing a significant health risk if disturbed. Lead-based paint, commonly found in older structures, can leach into the environment and cause developmental problems, particularly in children.
Remediation strategies involve careful assessment and removal of hazardous materials by licensed professionals. This process typically involves containment, careful removal, and proper disposal according to strict environmental regulations. For example, asbestos abatement requires specialized equipment and trained personnel to prevent the release of asbestos fibers into the air. Similarly, lead paint removal requires careful scraping and sanding, with proper ventilation and disposal procedures to minimize exposure.
Failure to address these hazards adequately can lead to severe health problems and significant legal liabilities. The EPA provides detailed guidance on asbestos and lead remediation.
Addressing Asbestos, Lead Paint, and Other Hazardous Materials
A comprehensive plan for addressing hazardous materials is paramount. This begins with a thorough environmental assessment conducted by a qualified professional. This assessment will identify the presence and extent of asbestos, lead paint, PCBs (polychlorinated biphenyls), and other potential contaminants. Based on the assessment, a remediation plan is developed, outlining the specific steps required for safe removal or encapsulation of hazardous materials.
This plan must comply with all applicable local, state, and federal regulations. The plan will specify the methods to be used, the protective equipment required for workers, and the disposal procedures for hazardous waste. For instance, asbestos removal often involves using specialized HEPA-filtered vacuum systems and containment strategies to prevent fiber dispersal. Lead paint abatement might involve techniques such as chemical stripping or careful sanding, followed by the application of a lead-safe primer and paint.
Detailed documentation of all remediation activities is essential for future reference and compliance.
Comparison of Factory and Residential Building Codes
Factory buildings are constructed to different codes than residential structures. Factory codes prioritize structural integrity and fire safety for industrial processes, often with less stringent requirements for insulation, soundproofing, or energy efficiency. Residential codes, on the other hand, emphasize comfort, habitability, and energy conservation. Converting a factory into a residence necessitates bringing the structure up to current residential building codes.
This might involve significant upgrades to insulation, HVAC systems, electrical wiring, plumbing, and fire safety features. Compliance with accessibility standards for people with disabilities is also crucial. The discrepancies between these codes often result in unforeseen costs and delays during the conversion process. Navigating these differences requires working closely with building inspectors and engineers to ensure compliance.
Potential Unexpected Costs Associated with Factory-to-Home Conversion
Renovating a factory into a home can incur unexpected costs beyond the initial estimates. These might include: unforeseen structural issues requiring extensive repairs; the discovery of hidden environmental hazards; delays caused by regulatory hurdles or permit applications; changes in material costs; and the need for specialized contractors with expertise in industrial building conversions. For instance, the discovery of hidden asbestos or lead paint can significantly increase remediation costs.
Unexpected structural problems, such as deteriorated beams or foundations, might require extensive repairs or reinforcements. These unexpected expenses highlight the importance of thorough due diligence, contingency planning, and securing adequate funding before embarking on such a project. It is advisable to include a substantial contingency buffer in the initial budget to account for these potential unforeseen circumstances.
A real-life example is the conversion of a former printing factory in Brooklyn, where the initial budget had to be significantly increased due to the discovery of extensive asbestos contamination.
Architectural Design Considerations
Transforming a raw industrial space into a comfortable and functional home requires careful architectural planning. The inherent characteristics of a factory—high ceilings, exposed brick, large windows (often strategically placed for maximum natural light, though sometimes absent), and expansive floor plans—present both opportunities and challenges for residential conversion. Successful projects prioritize maximizing natural light, integrating existing structural elements, and strategically incorporating modern amenities while maintaining the building’s industrial aesthetic.
Floor Plan Design for Factory Conversion
A successful floor plan balances open and private spaces, leveraging the factory’s existing structure. Imagine a 10,000 square foot factory. The original layout might have been a vast open area with supporting columns. A redesigned floor plan could incorporate a large, open-plan living, dining, and kitchen area in the central space, utilizing the height for a double-height ceiling to emphasize the volume and maximize natural light.
Private spaces, such as bedrooms and bathrooms, could be created by strategically placing partitions, perhaps utilizing reclaimed factory materials. A master suite, incorporating a large walk-in closet and ensuite bathroom, could occupy one wing, while guest bedrooms and a shared bathroom could be situated in another. A home office or studio could be carved out of a quieter area, perhaps near existing loading docks that can be repurposed as windows or skylights.
The original structure’s integrity should guide the partition placement, respecting load-bearing walls and structural columns.
Integration of Original Factory Features
Preserving and showcasing original factory features adds character and historical context. Exposed brick walls, polished concrete floors, and high ceilings are all hallmarks of industrial architecture. These features can be enhanced, not hidden. For example, the exposed brick could be cleaned and sealed to preserve its texture and color. The concrete floor could be polished to a high sheen, creating a modern and durable surface.
Original structural steel beams could be painted a contrasting color to highlight them as design elements. Large, industrial-style windows, if present, could be restored and used to flood the space with natural light. Existing machinery or equipment, if structurally sound and aesthetically pleasing, could be repurposed as unique design elements. A vintage crane, for instance, could become a striking focal point in the living area.
Examples of Successful Factory-to-Home Conversions
Numerous successful conversions demonstrate creative design choices. One notable example is the conversion of a former textile mill in Massachusetts. The architects retained the original exposed brick walls and wooden beams, creating a rustic-industrial aesthetic. Large windows were added to maximize natural light, and a modern kitchen and bathrooms were seamlessly integrated, using materials that complemented the existing structure.
Another example is a former warehouse in Brooklyn, New York, converted into a loft-style apartment. The high ceilings and expansive open floor plan were retained, while private spaces were created using glass partitions to maintain a sense of openness. The use of reclaimed wood and metal throughout the space further enhanced the industrial aesthetic. These examples demonstrate the potential to create unique and stylish homes while respecting the historical significance of the original structures.
Maximizing Natural Light in Factory Conversions
Factories, often designed for functionality rather than aesthetics, may lack ample natural light. Strategic interventions can rectify this. Large windows, skylights, and even light wells can be installed to introduce natural light into previously dark areas. The placement of these light sources should be carefully considered to optimize light distribution throughout the space. Light-colored walls and floors will reflect light, enhancing brightness.
The use of translucent partitions between rooms can also help to distribute natural light more effectively. In some cases, the removal of non-structural walls can open up the space and allow for more natural light penetration. Consider the sun’s path and the orientation of the building when planning the placement of new windows and skylights.
Incorporating Modern Amenities While Preserving Historical Elements
Integrating modern amenities requires careful planning to avoid disrupting the existing structure’s character. Kitchens and bathrooms, for instance, can be designed to blend seamlessly with the industrial aesthetic. Using materials such as stainless steel, concrete, and reclaimed wood can create a cohesive look. Modern appliances can be integrated into custom cabinetry to maintain a clean and uncluttered appearance.
Bathrooms can incorporate industrial-style fixtures and finishes, such as exposed plumbing and concrete countertops. The key is to select materials and finishes that complement the existing architecture rather than clashing with it. This careful selection ensures that the historical elements remain the focal points, while modern conveniences are seamlessly integrated into the space.
Engineering and Infrastructure
Transforming a derelict factory into a comfortable home requires a comprehensive overhaul of its engineering and infrastructure. This involves upgrading outdated systems to meet modern residential standards, while simultaneously addressing the unique challenges presented by the building’s industrial past. The process necessitates careful planning, precise execution, and adherence to stringent building codes.
Electrical System Upgrade
The electrical system of a factory is typically designed for heavy industrial loads, often utilizing high-voltage three-phase power. Converting this to a residential system requires a complete rewire. This involves replacing existing wiring with appropriately sized conductors for residential loads, installing new circuit breakers and panels compliant with current building codes, and ensuring proper grounding and safety measures are in place.
For example, a factory might have a 480-volt, three-phase system; this would need to be stepped down to a standard 120/240-volt, single-phase system for residential use, often requiring the installation of a new transformer. Careful consideration must be given to the placement of outlets and lighting fixtures to meet the needs of a modern home, potentially requiring trenching and conduit installation.
Plumbing and Sewage System Installation
Factories rarely possess residential-grade plumbing and sewage systems. Installing these necessitates running new water lines from the main supply, ensuring sufficient water pressure for showers, toilets, and appliances. This may involve significant excavation and the installation of new pipes, potentially including pressure-testing to ensure leak-free operation. The sewage system requires connecting to the municipal sewer line, which may involve navigating existing underground infrastructure and adhering to strict regulations concerning wastewater discharge.
Wastewater treatment might also require additional considerations if the factory’s existing system is inadequate. For instance, greywater recycling systems could be integrated to conserve water and reduce environmental impact.
Insulation and Energy Efficiency Improvements
Factory buildings often lack adequate insulation, resulting in significant energy loss. Improving energy efficiency requires a multi-pronged approach. This includes installing high-performance insulation in walls, ceilings, and floors, using materials such as spray foam, rigid foam boards, or mineral wool. Air sealing is crucial to prevent drafts and air leakage, which can be achieved through caulking, weatherstripping, and the installation of vapor barriers.
High-efficiency windows and doors should replace existing industrial-grade openings. Furthermore, incorporating passive solar design elements can further reduce energy consumption. For instance, strategically placed windows can maximize natural light and reduce the need for artificial lighting.
HVAC System Enhancement
Factory HVAC systems, if present, are usually designed for industrial conditions and may not be suitable for residential comfort. A complete overhaul might be necessary, installing a zoned heating and cooling system to regulate temperatures in different areas of the house effectively. High-efficiency heat pumps or furnaces, coupled with well-insulated ductwork, are essential for optimal energy performance. Proper ventilation is critical for indoor air quality, requiring the installation of exhaust fans in bathrooms and kitchens, and potentially a whole-house ventilation system to remove stale air and introduce fresh air.
The choice of HVAC system should consider the climate and the size of the converted space.
Structural Reinforcement
Factories are built for strength and durability, but their structural elements may not be optimally suited for residential use. Reinforcing the structure may be necessary to meet residential building codes and ensure the safety and stability of the building. This could involve strengthening existing load-bearing walls, columns, and beams, possibly through the addition of steel supports or concrete reinforcement.
The foundation might also require inspection and reinforcement, depending on its condition and the intended residential use. Seismic upgrades might be necessary in earthquake-prone areas. A thorough structural engineering assessment is crucial before commencing any renovations.
Cost Comparison of System Upgrades
System | Estimated Cost Range (USD) | Factors Affecting Cost | Example Scenario |
---|---|---|---|
Electrical | $10,000 – $50,000+ | Size of building, complexity of rewiring, need for new panel and service upgrade | A 5,000 sq ft factory requiring a complete rewire and new service could cost $30,000 – $40,000 |
Plumbing & Sewage | $15,000 – $40,000+ | Existing infrastructure, length of new lines, complexity of connections | A renovation requiring extensive new plumbing and sewer lines could cost $25,000 – $35,000 |
Insulation & Energy Efficiency | $5,000 – $20,000+ | Size of building, type of insulation used, window and door replacements | Adding spray foam insulation and replacing all windows in a 3,000 sq ft factory could cost $10,000 – $15,000 |
HVAC | $10,000 – $30,000+ | Size of building, type of system installed, ductwork installation | Installing a new high-efficiency heat pump system in a 4,000 sq ft factory could cost $15,000 – $25,000 |
Structural Reinforcement | $5,000 – $50,000+ | Extent of necessary repairs, materials used, engineering fees | Reinforcing load-bearing walls and foundation in a large factory could cost $20,000 – $40,000 |
Interior Design and Aesthetics
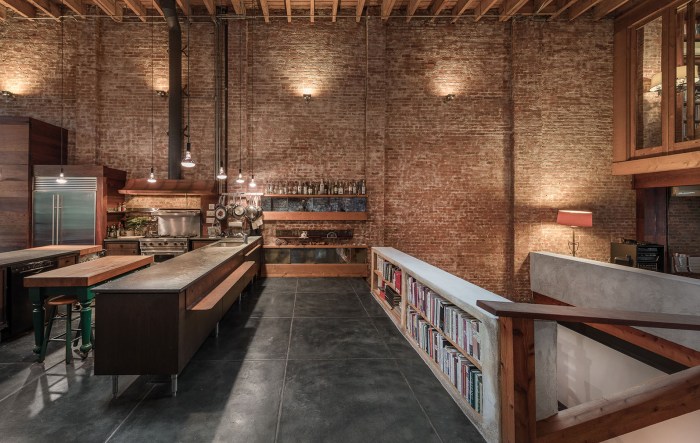
Transforming a raw, industrial factory into a comfortable and stylish home requires a delicate balance between preserving the building’s inherent character and creating a livable space. The aesthetic appeal hinges on successfully integrating the rugged charm of the original structure with modern design elements to achieve a unique and inviting atmosphere.The inherent textural contrasts and the visual history embedded within the factory’s original features offer a compelling foundation for interior design.
The Aesthetic Appeal of Industrial Elements
Exposed brick, metal beams, and concrete floors, hallmarks of industrial architecture, possess a raw, authentic beauty. The exposed brick, often showing variations in color and texture, provides a sense of warmth and history, counterbalancing the coolness of the metal and concrete. Metal beams, typically steel or iron, add a strong linear element, creating visual interest and highlighting the building’s structural integrity.
The concrete floors, often polished or stained, contribute a sense of spaciousness and durability. This combination of materials creates a visually rich and dynamic space, characterized by a juxtaposition of textures and a sense of authenticity rarely found in conventional homes. The psychological effect of these materials is often described as fostering a sense of openness, strength, and historical connection.
Suitable Color Palettes and Materials
A successful color palette for a factory conversion often utilizes a neutral base, allowing the industrial elements to take center stage. Shades of gray, charcoal, and beige work well, providing a backdrop that complements the exposed brick and metal. Accents of bolder colors, such as deep blues, greens, or rusts, can be introduced through furniture, artwork, or textiles, adding warmth and personality.
Materials like reclaimed wood, leather, and metal are ideal choices, echoing the industrial aesthetic while adding layers of texture and visual interest. Consider incorporating natural elements, such as plants and stone, to soften the industrial feel and introduce a touch of nature. For example, a palette might feature a base of warm gray walls, complemented by dark wood flooring, black metal accents, and pops of deep teal in upholstery and artwork.
Incorporating Modern Furniture and Decor
Modern furniture and decor can seamlessly integrate with the industrial aesthetic. Clean lines and minimalist designs are often preferred, preventing the space from feeling cluttered. The contrast between sleek, modern furniture and the rough texture of the exposed brick creates a sophisticated and visually appealing tension. Materials like glass, chrome, and polished wood can complement the industrial elements, while plush textiles, such as velvet or linen, add comfort and warmth.
Strategically placed artwork, sculptural elements, and carefully chosen accessories can further personalize the space and add layers of visual complexity. For example, a minimalist white sofa might be paired with a vintage industrial-style coffee table and a collection of modern abstract art.
Mood Board Description
The mood board would depict a space that balances industrial grit with modern sophistication. The color palette would center around a muted gray base, with accents of deep teal and warm brass. Textures would include the rough texture of exposed brick, the smooth coolness of polished concrete, the warmth of reclaimed wood, and the softness of plush velvet upholstery.
The overall style would be a blend of industrial and minimalist, with clean lines and a focus on showcasing the unique architectural features of the converted factory. The mood board would feature images of exposed brick walls, polished concrete floors, sleek modern furniture, industrial lighting fixtures, and carefully selected artwork and accessories that reflect the chosen color palette and textures.
The overall atmosphere would be one of refined industrial chic, balancing the raw energy of the original structure with a sense of calm and sophistication.
Lighting Plan
Lighting plays a crucial role in highlighting the unique features of a converted factory. A layered approach is key, incorporating ambient, task, and accent lighting to create a dynamic and inviting atmosphere. Ambient lighting, provided by recessed fixtures or pendant lights, establishes a general illumination level. Task lighting, such as desk lamps or floor lamps, provides focused light for specific activities.
Accent lighting, using track lighting or spotlights, draws attention to the exposed brick, metal beams, and other architectural details. Consider incorporating industrial-style pendant lights above the kitchen island or dining table, and using track lighting to highlight artwork or architectural features. The strategic use of lighting can transform the space, enhancing its character and creating a warm and welcoming environment.
Permitting and Legal Considerations
Transforming a derelict factory into a habitable residence presents a unique set of legal and permitting hurdles. Navigating these complexities requires meticulous planning and a thorough understanding of local regulations. Failure to comply can lead to significant delays, financial penalties, and even project termination. This section details the crucial legal aspects of such a conversion.
Necessary Permits and Approvals
Securing the necessary permits is paramount. The specific permits will vary depending on location and the extent of the renovation, but generally include demolition permits (if applicable), building permits encompassing structural modifications, electrical work, plumbing, and HVAC installations, and occupancy permits signifying the building’s readiness for habitation. Furthermore, depending on the scale and nature of the changes, permits related to environmental remediation (asbestos abatement, lead paint removal) may be necessary.
Each permit application necessitates detailed plans, specifications, and often, engineering reports. The process often involves multiple inspections at various stages of construction by relevant authorities to ensure compliance with building codes and safety regulations. For example, a major structural alteration would require detailed structural engineering calculations and plans submitted with the building permit application.
Zoning Regulations and Building Codes
Zoning regulations dictate the permissible land use within a specific area. Converting a factory, typically zoned for industrial use, into a residential dwelling often necessitates a zoning variance or rezoning application. This process typically involves a public hearing and demonstrates that the conversion aligns with the overall zoning plan and doesn’t negatively impact the surrounding community. Building codes, on the other hand, establish minimum standards for structural integrity, fire safety, accessibility, and other aspects of building construction and safety.
These codes often have stricter requirements for residential buildings compared to industrial structures. Compliance necessitates modifications to meet these standards, which might include upgrades to insulation, electrical systems, and fire suppression systems. For instance, a factory’s existing electrical system might not meet the current residential code for amperage and circuit protection, requiring complete overhaul.
Financing for Factory Conversions
Securing financing for such a unique project can be challenging. Traditional lenders may be hesitant due to the inherent complexities and potential risks associated with converting an industrial building. A detailed and comprehensive renovation plan, along with realistic budget projections and a thorough assessment of potential environmental liabilities, is crucial to secure funding. Exploring alternative financing options, such as private loans or construction-to-permanent loans, might be necessary.
Demonstrating a clear understanding of the project’s financial feasibility and providing evidence of sufficient equity can significantly improve the chances of securing financing. For example, a detailed cost breakdown, including materials, labor, permits, and contingency funds, presented to potential lenders will bolster the application’s strength.
Potential Legal Challenges and Proactive Measures
Legal challenges can arise from various sources, including environmental contamination, historical preservation concerns, and disputes with neighbors. Proactive measures are essential to mitigate these risks. Thorough environmental assessments should be conducted early in the process to identify and address potential contamination issues. If the factory is located in a historical district, working closely with historical preservation authorities is crucial to ensure compliance with preservation regulations.
Engaging in open communication with neighbors and addressing their concerns can prevent potential disputes. Detailed documentation of all permits, inspections, and communications with authorities provides a strong legal defense against potential challenges. For instance, documenting the asbestos abatement process, including lab reports and disposal records, protects against future liability.
Checklist of Legal Requirements and Deadlines
Prior to commencing any work, a comprehensive checklist should be created, tailored to the specific project. This checklist should include: Securing all necessary permits (demolition, building, occupancy, environmental remediation); Compliance with zoning regulations and building codes; Securing financing; Conducting environmental assessments; Addressing historical preservation concerns; Establishing clear communication channels with neighbors and authorities; Regularly monitoring deadlines for permit applications, inspections, and other legal requirements.
Each item should have a corresponding deadline and assigned responsible party. Regularly reviewing and updating this checklist ensures the project remains on track and minimizes legal risks. For example, a realistic timeline should be set for each permit application, factoring in processing times and potential delays.
Last Word
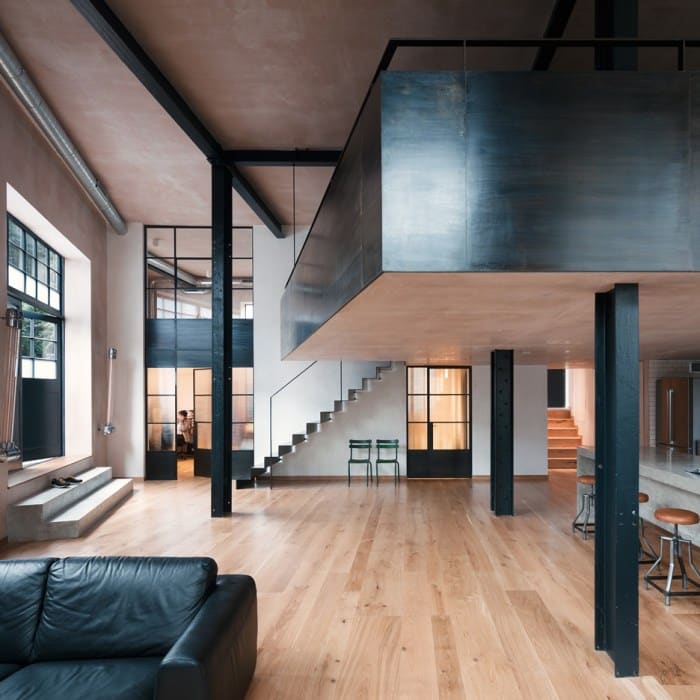
Renovating a factory into a home is a testament to human ingenuity and a celebration of adaptive reuse. The process, though demanding, offers unparalleled opportunities for creating unique and character-filled living spaces. By carefully addressing the structural, environmental, and design considerations Artikeld, homeowners can successfully transform a relic of industrial history into a modern, comfortable, and aesthetically stunning residence.
The careful planning and execution detailed throughout this guide provide a roadmap for navigating this challenging yet rewarding endeavor, ultimately resulting in a home that reflects both the building’s industrial past and its vibrant new future. The successful conversion showcases not only the triumph of architectural design but also the power of sustainable practices in repurposing existing structures.
Quick FAQs
What are the typical lifespan extensions after such a renovation?
With proper remediation and reinforcement, a renovated factory can achieve a lifespan comparable to a newly constructed home, potentially exceeding 50 years or more, depending on materials and maintenance.
How does insurance coverage differ for factory conversions?
Insurance premiums may be higher initially due to the unique risks associated with repurposing a factory. Detailed inspections and comprehensive coverage are crucial. Consult with multiple insurers for the best rates.
What about noise pollution from nearby industrial areas?
Noise mitigation strategies, such as soundproof windows and insulation, are vital. Pre-purchase assessments of ambient noise levels are recommended.
Are there specific grants or tax incentives available for this type of renovation?
Depending on location and the project’s specifics (e.g., energy efficiency upgrades, historical preservation), various local, state, and federal incentives may be available. Research local programs thoroughly.
Can I use the existing factory’s foundation as is?
The existing foundation’s suitability depends on its condition and the new home’s design load. A structural engineer’s assessment is crucial to determine if it needs reinforcement or replacement.